Destylator przemysłowy
Destylator przemysłowy to urządzenie, które odgrywa kluczową rolę w procesach separacji i oczyszczania cieczy. Jego działanie opiera się na różnicy temperatur wrzenia substancji, co pozwala na oddzielenie składników mieszaniny. W przemyśle chemicznym, farmaceutycznym czy petrochemicznym destylatory są wykorzystywane do produkcji czystych substancji chemicznych, a także do odzyskiwania rozpuszczalników. Proces destylacji może być przeprowadzany w różnych warunkach, w zależności od rodzaju materiału oraz wymagań dotyczących jakości produktu końcowego. W destylatorze przemysłowym często stosuje się kolumny destylacyjne, które umożliwiają wielokrotne parowanie i skraplanie, co zwiększa efektywność procesu. Oprócz tego, nowoczesne destylatory są wyposażone w zaawansowane systemy kontroli, które monitorują temperaturę, ciśnienie oraz inne parametry, co pozwala na optymalizację procesu i minimalizację strat surowców.
Jakie są zastosowania destylatora przemysłowego w różnych branżach
Destylator przemysłowy znajduje szerokie zastosowanie w wielu branżach, co czyni go niezbędnym narzędziem w procesach produkcyjnych. W przemyśle chemicznym służy do separacji i oczyszczania różnych substancji chemicznych, takich jak alkohole, kwasy czy estry. W branży petrochemicznej destylatory są wykorzystywane do rafinacji ropy naftowej, gdzie oddziela się różne frakcje węglowodorowe, takie jak benzyna, olej napędowy czy nafta. W przemyśle spożywczym destylacja jest kluczowym procesem przy produkcji napojów alkoholowych, takich jak whisky czy wódka, gdzie celem jest uzyskanie odpowiedniej czystości i smaku trunku. Dodatkowo, w farmaceutyce destylatory służą do oczyszczania substancji czynnych oraz rozpuszczalników używanych w produkcji leków. W ostatnich latach rośnie również zainteresowanie wykorzystaniem destylacji w procesach związanych z ochroną środowiska, takich jak oczyszczanie ścieków czy odzyskiwanie cennych surowców z odpadów.
Jakie są kluczowe elementy konstrukcyjne destylatora przemysłowego
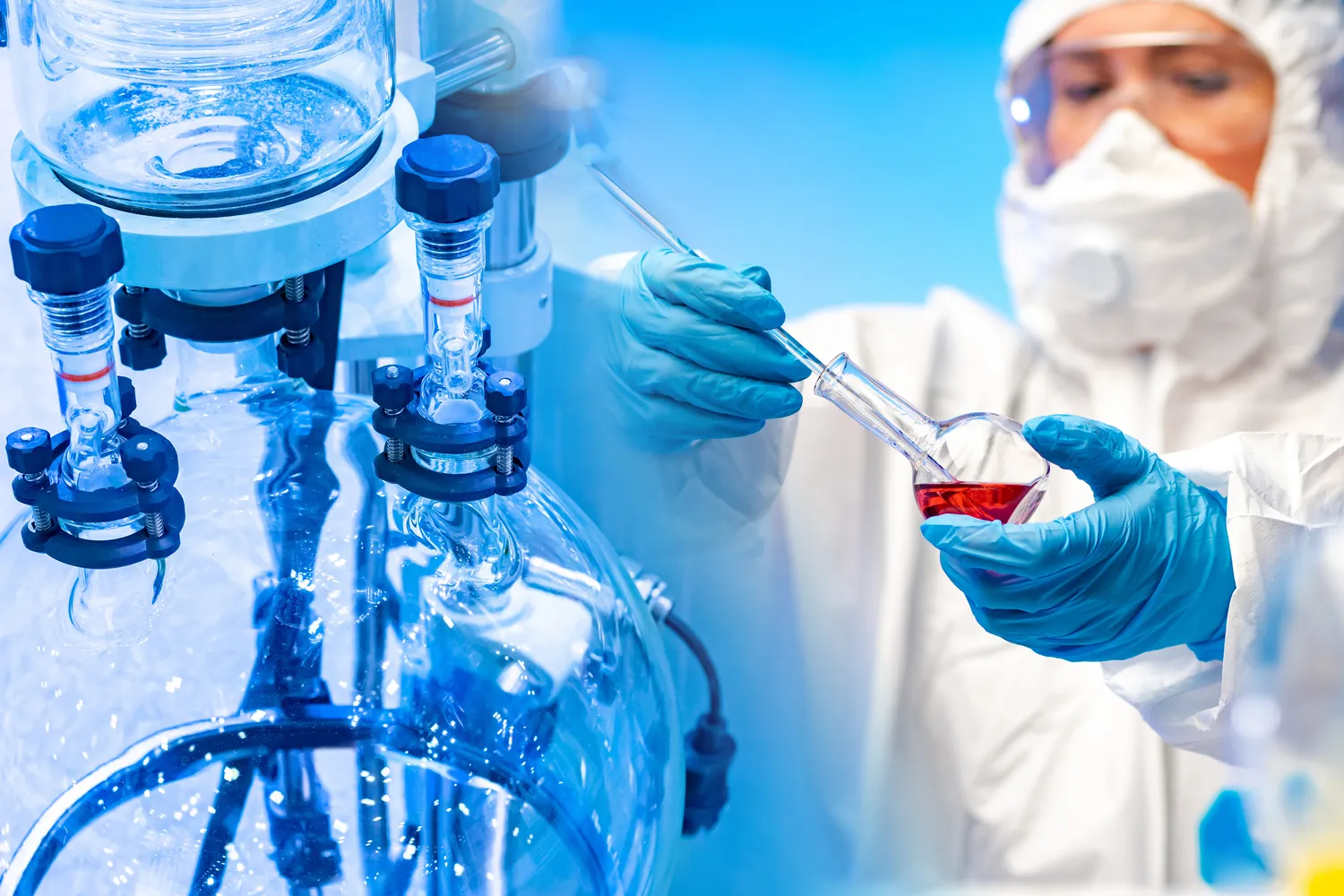
Konstrukcja destylatora przemysłowego składa się z kilku kluczowych elementów, które współpracują ze sobą w celu efektywnego przeprowadzenia procesu destylacji. Podstawowym komponentem jest zbiornik do gotowania, gdzie umieszczana jest mieszanina cieczy do destylacji. Zbiornik ten jest zazwyczaj podgrzewany za pomocą grzałek elektrycznych lub pary wodnej. Kolejnym istotnym elementem jest kolumna destylacyjna, która umożliwia wielokrotne parowanie i skraplanie składników mieszaniny. Kolumna ta może być wyposażona w różnego rodzaju packingi lub talerze, które zwiększają powierzchnię kontaktu między parą a cieczą. Po przejściu przez kolumnę para trafia do kondensatora, gdzie zostaje schłodzona i skroplona do postaci cieczy. Oprócz tych głównych komponentów ważne są również systemy kontrolne oraz pompy transportowe, które zapewniają odpowiedni przepływ cieczy oraz monitorują parametry pracy urządzenia.
Jakie są korzyści z używania nowoczesnych destylatorów przemysłowych
Nowoczesne destylatory przemysłowe oferują szereg korzyści, które znacząco poprawiają efektywność procesów produkcyjnych oraz jakość uzyskiwanych produktów. Przede wszystkim dzięki zastosowaniu zaawansowanych technologii kontrolnych możliwe jest precyzyjne monitorowanie parametrów pracy urządzenia, co pozwala na optymalizację procesu i minimalizację strat surowców. Nowoczesne modele często charakteryzują się wyższą wydajnością energetyczną dzięki zastosowaniu innowacyjnych rozwiązań konstrukcyjnych oraz materiałowych. Ponadto wiele nowoczesnych destylatorów jest zaprojektowanych z myślą o łatwej konserwacji i serwisowaniu, co przekłada się na mniejsze przestoje w produkcji oraz niższe koszty eksploatacji. Warto również zauważyć, że nowoczesne technologie umożliwiają stosowanie bardziej ekologicznych metod produkcji oraz odzyskiwania surowców z odpadów. Dzięki temu przedsiębiorstwa mogą nie tylko zwiększać swoją konkurencyjność na rynku, ale także przyczyniać się do ochrony środowiska poprzez zmniejszenie negatywnego wpływu swojej działalności na otoczenie.
Jakie są różnice między destylatorami przemysłowymi a laboratoryjnymi
Destylatory przemysłowe i laboratoryjne różnią się pod wieloma względami, co wpływa na ich zastosowanie oraz konstrukcję. Przede wszystkim destylatory przemysłowe są zaprojektowane do pracy w dużej skali, co oznacza, że są w stanie przetwarzać znacznie większe ilości cieczy niż ich odpowiedniki laboratoryjne. W związku z tym, ich konstrukcja jest bardziej masywna i wytrzymała, aby sprostać wymaganiom intensywnej eksploatacji. W laboratoriach natomiast często stosuje się mniejsze urządzenia, które są bardziej mobilne i łatwiejsze w obsłudze. Kolejną różnicą jest stopień automatyzacji – destylatory przemysłowe zazwyczaj wyposażone są w zaawansowane systemy automatyki, które umożliwiają zdalne monitorowanie i kontrolowanie procesów, podczas gdy w laboratoriach często wymagana jest ręczna obsługa. Różnice te obejmują również zastosowane materiały – w przemyśle preferuje się materiały odporne na korozję oraz wysokie temperatury, natomiast w laboratoriach można stosować bardziej delikatne komponenty.
Jakie są najnowsze trendy w technologii destylacji przemysłowej
W ostatnich latach technologia destylacji przemysłowej przechodzi dynamiczne zmiany, które mają na celu zwiększenie efektywności procesów oraz minimalizację wpływu na środowisko. Jednym z najważniejszych trendów jest rozwój technologii odzyskiwania ciepła, która pozwala na wykorzystanie energii cieplnej generowanej podczas procesu destylacji do podgrzewania innych części systemu. Dzięki temu możliwe jest znaczne obniżenie kosztów operacyjnych oraz zmniejszenie zużycia energii. Innym istotnym kierunkiem rozwoju jest automatyzacja procesów, która pozwala na zdalne monitorowanie i zarządzanie pracą destylatorów. Systemy te często wykorzystują sztuczną inteligencję do analizy danych i optymalizacji parametrów pracy urządzenia w czasie rzeczywistym. Warto również zauważyć rosnące zainteresowanie ekologicznymi metodami produkcji, takimi jak wykorzystanie biomasy czy recykling rozpuszczalników. Firmy coraz częściej inwestują w technologie, które pozwalają na zmniejszenie emisji gazów cieplarnianych oraz ograniczenie zużycia surowców naturalnych.
Jakie są koszty zakupu i eksploatacji destylatora przemysłowego
Koszty zakupu i eksploatacji destylatora przemysłowego mogą znacznie się różnić w zależności od wielu czynników, takich jak typ urządzenia, jego wydajność oraz zastosowane technologie. Na początku warto zwrócić uwagę na koszty zakupu samego urządzenia, które mogą wynosić od kilku tysięcy do nawet milionów złotych w przypadku dużych instalacji przemysłowych. Dodatkowo należy uwzględnić koszty montażu oraz uruchomienia systemu, które mogą być znaczące zwłaszcza w przypadku bardziej skomplikowanych instalacji. Kolejnym istotnym aspektem są koszty eksploatacyjne, które obejmują zużycie energii elektrycznej lub pary wodnej potrzebnej do podgrzewania cieczy oraz koszty konserwacji i serwisowania urządzenia. Warto również pamiętać o kosztach związanych z zakupem surowców oraz ewentualnymi kosztami związanymi z utylizacją odpadów powstających podczas procesu destylacji.
Jakie są kluczowe czynniki wpływające na wybór destylatora przemysłowego
Wybór odpowiedniego destylatora przemysłowego to decyzja, która powinna być dokładnie przemyślana i oparta na kilku kluczowych czynnikach. Po pierwsze, należy określić rodzaj substancji, które będą poddawane procesowi destylacji oraz ich właściwości fizyczne i chemiczne. Różne substancje mogą wymagać różnych podejść do procesu separacji, dlatego ważne jest dobranie odpowiedniej technologii. Kolejnym czynnikiem jest wydajność urządzenia – należy określić ilość materiału, która będzie przetwarzana w danym czasie oraz wymagania dotyczące jakości produktu końcowego. Ważne jest także uwzględnienie dostępnej przestrzeni oraz infrastruktury zakładu produkcyjnego, co może wpłynąć na wybór konkretnego modelu destylatora. Koszt zakupu oraz eksploatacji również odgrywa kluczową rolę w podejmowaniu decyzji – warto porównać różne oferty rynkowe oraz przeanalizować potencjalne oszczędności wynikające z użytkowania danego urządzenia.
Jakie są wyzwania związane z eksploatacją destylatorów przemysłowych
Eksploatacja destylatorów przemysłowych wiąże się z szeregiem wyzwań, które mogą wpływać na efektywność procesu oraz jakość uzyskiwanych produktów. Jednym z głównych problemów jest utrzymanie optymalnych warunków pracy urządzenia – niewłaściwe ustawienia temperatury czy ciśnienia mogą prowadzić do obniżenia wydajności lub zanieczyszczenia produktu końcowego. Ponadto regularna konserwacja i serwisowanie są niezbędne do zapewnienia długotrwałej niezawodności sprzętu; zaniedbania w tym zakresie mogą prowadzić do kosztownych awarii i przestojów produkcyjnych. Kolejnym wyzwaniem jest zarządzanie odpadami powstającymi podczas procesu destylacji; konieczne jest wdrożenie skutecznych metod ich utylizacji lub recyklingu zgodnie z obowiązującymi normami ekologicznymi. Warto również zwrócić uwagę na rosnące wymagania regulacyjne dotyczące ochrony środowiska oraz bezpieczeństwa pracy; przedsiębiorstwa muszą dostosować swoje procesy do tych norm, co może wiązać się z dodatkowymi kosztami i inwestycjami w technologie przyjazne dla środowiska.
Jakie są przyszłościowe kierunki rozwoju technologii destylacji
Przyszłość technologii destylacji zapowiada się obiecująco dzięki dynamicznemu rozwojowi innowacyjnych rozwiązań technologicznych oraz rosnącemu naciskowi na zrównoważony rozwój. Jednym z kluczowych kierunków rozwoju będzie dalsza automatyzacja procesów produkcyjnych; inteligentne systemy zarządzania oparte na sztucznej inteligencji będą coraz częściej wykorzystywane do optymalizacji parametrów pracy destylatorów oraz monitorowania ich stanu technicznego w czasie rzeczywistym. Równocześnie wzrośnie znaczenie ekologicznych metod produkcji; technologie takie jak odzyskiwanie ciepła czy zastosowanie odnawialnych źródeł energii staną się standardem w branży chemicznej i petrochemicznej. Innowacje będą także dotyczyć materiałów używanych do budowy destylatorów; nowe kompozyty i materiały odporne na korozję pozwolą na zwiększenie trwałości urządzeń oraz obniżenie kosztów ich eksploatacji. Warto również zauważyć rosnącą popularność mikrodestylacji; ta technologia umożliwia przeprowadzanie procesów separacji na małą skalę przy zachowaniu wysokiej efektywności energetycznej i jakości produktu końcowego.