Destylacja rozpuszczalników
Destylacja rozpuszczalników to proces, który polega na oddzieleniu składników mieszaniny na podstawie różnicy ich temperatur wrzenia. W tym procesie najpierw podgrzewa się ciecz, co powoduje jej parowanie. Para, która powstaje, jest następnie schładzana i kondensowana z powrotem do stanu ciekłego. Kluczowym elementem tego procesu jest kolumna destylacyjna, która umożliwia wielokrotne skraplanie i parowanie, co prowadzi do uzyskania wyższej czystości produktu końcowego. W praktyce destylacja rozpuszczalników jest szeroko stosowana w przemyśle chemicznym oraz farmaceutycznym, gdzie czystość substancji ma kluczowe znaczenie. Ważne jest również, aby zrozumieć różnice między destylacją prostą a frakcyjną. Destylacja prosta stosowana jest w przypadku jednofazowych mieszanin, podczas gdy destylacja frakcyjna znajduje zastosowanie w bardziej złożonych systemach, gdzie składniki mają zbliżone temperatury wrzenia.
Jakie są zastosowania destylacji rozpuszczalników w przemyśle
Destylacja rozpuszczalników ma wiele zastosowań w różnych branżach przemysłowych. Przede wszystkim jest kluczowym procesem w produkcji chemikaliów, gdzie czystość surowców i produktów końcowych ma ogromne znaczenie. W przemyśle petrochemicznym destylacja służy do separacji różnych frakcji ropy naftowej, co pozwala na uzyskanie paliw oraz innych produktów chemicznych o określonych właściwościach. W branży farmaceutycznej proces ten jest wykorzystywany do oczyszczania substancji czynnych oraz rozpuszczalników używanych w produkcji leków. Dodatkowo destylacja rozpuszczalników znajduje zastosowanie w przemyśle spożywczym, gdzie może być używana do ekstrakcji aromatów lub konserwantów. Warto również wspomnieć o rosnącej popularności destylacji w produkcji alkoholu, gdzie proces ten pozwala na uzyskanie wysokiej jakości napojów spirytusowych poprzez eliminację niepożądanych składników.
Jakie są najważniejsze rodzaje destylacji rozpuszczalników
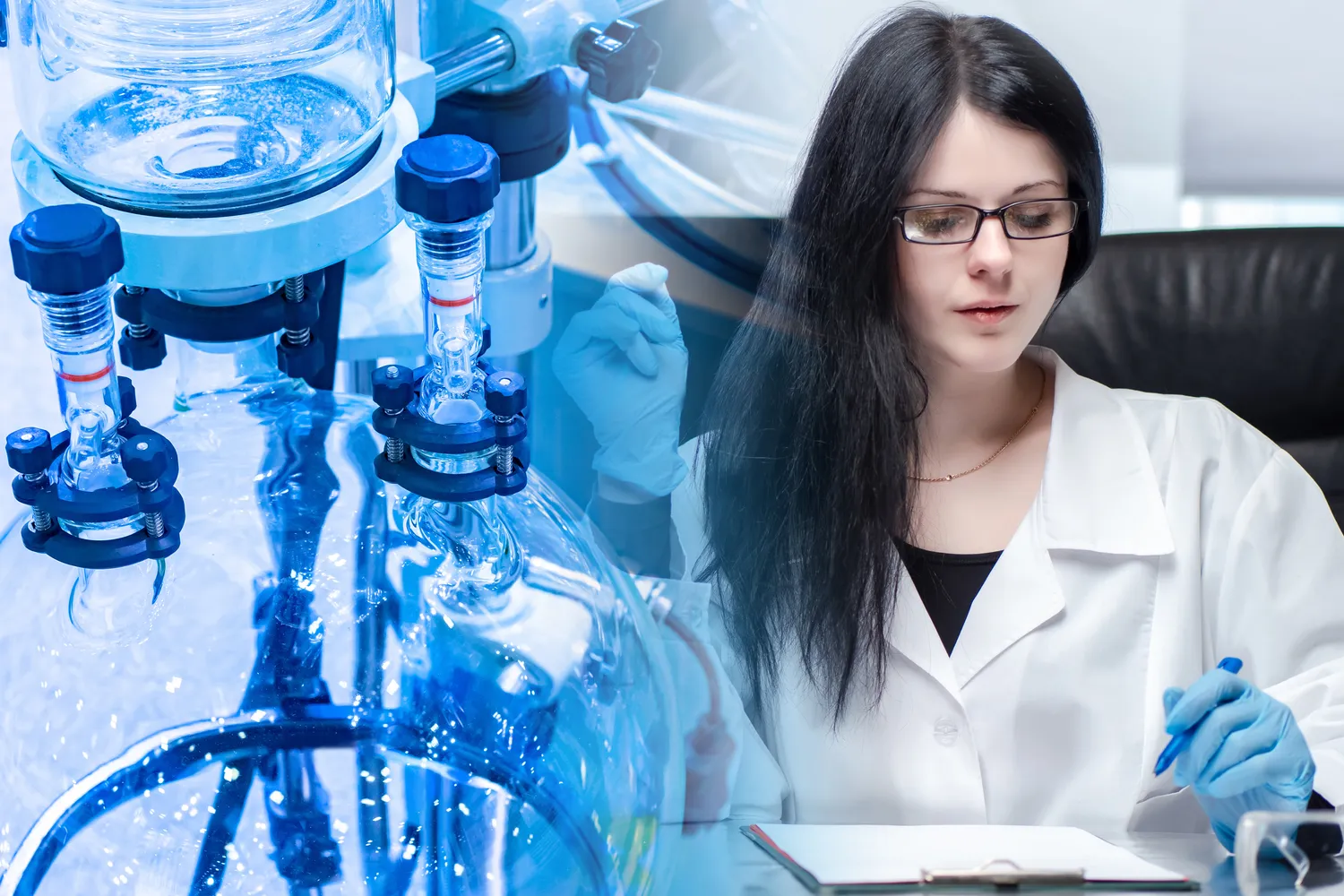
W kontekście destylacji rozpuszczalników wyróżnia się kilka podstawowych rodzajów tego procesu, które mają swoje specyficzne zastosowania oraz zalety. Najbardziej znaną formą jest destylacja prosta, która polega na jednorazowym podgrzewaniu cieczy i skraplaniu powstałej pary. Jest to metoda stosunkowo łatwa do przeprowadzenia, jednak jej efektywność ogranicza się do mieszanin o znacznej różnicy temperatur wrzenia składników. Kolejnym rodzajem jest destylacja frakcyjna, która wykorzystuje kolumny frakcyjne do wielokrotnego parowania i skraplania, co pozwala na uzyskanie wyższej czystości produktów. Istnieje również destylacja azeotropowa, która ma zastosowanie w przypadku mieszanin tworzących azeotropy – substancje te mają stały skład w stanie ciekłym i nie można ich oddzielić za pomocą tradycyjnej destylacji. Dodatkowo wyróżnia się także destylację próżniową, która odbywa się w obniżonym ciśnieniu i umożliwia separację składników o wysokich temperaturach wrzenia bez ich degradacji.
Jakie są zalety i wady różnych metod destylacji rozpuszczalników
Każda metoda destylacji rozpuszczalników ma swoje zalety oraz wady, które należy uwzględnić przy wyborze odpowiedniej technologii dla danego procesu przemysłowego. Destylacja prosta charakteryzuje się prostotą wykonania oraz niskimi kosztami inwestycyjnymi związanymi z aparaturą. Jednak jej ograniczona efektywność sprawia, że nie nadaje się do separacji składników o zbliżonych temperaturach wrzenia. Z kolei destylacja frakcyjna oferuje znacznie wyższą wydajność i czystość produktów końcowych dzięki zastosowaniu kolumn frakcyjnych, ale wiąże się z większymi kosztami operacyjnymi oraz bardziej skomplikowanym procesem technologicznym. Destylacja azeotropowa pozwala na skuteczne oddzielanie mieszanin azeotropowych, ale wymaga stosowania dodatkowych substancji chemicznych lub zmiany warunków procesu, co może zwiększać koszty produkcji. Natomiast destylacja próżniowa umożliwia separację składników o wysokich temperaturach wrzenia bez ich degradacji, co jest istotne w przypadku delikatnych substancji chemicznych.
Jakie są najczęstsze błędy podczas destylacji rozpuszczalników
Podczas przeprowadzania procesu destylacji rozpuszczalników mogą wystąpić różne błędy, które mogą wpłynąć na efektywność oraz jakość uzyskiwanych produktów. Jednym z najczęstszych problemów jest niewłaściwe ustawienie temperatury. Zbyt niska temperatura może prowadzić do niepełnej separacji składników, co skutkuje zanieczyszczeniem produktu końcowego. Z kolei zbyt wysoka temperatura może prowadzić do degradacji wrażliwych substancji chemicznych, co również negatywnie wpływa na jakość. Kolejnym błędem jest niewłaściwe dobranie sprzętu, takiego jak kolumna destylacyjna czy chłodnica. Użycie niewłaściwego typu kolumny może ograniczyć efektywność procesu, a także prowadzić do strat materiałowych. Ponadto, nieodpowiednie zarządzanie ciśnieniem w systemie może wpłynąć na temperatury wrzenia składników, co również może skutkować nieefektywną separacją. Warto również zwrócić uwagę na czystość używanych surowców oraz sprzętu, ponieważ zanieczyszczenia mogą wprowadzać dodatkowe składniki do procesu, co obniża jakość końcowego produktu.
Jakie są nowoczesne technologie w destylacji rozpuszczalników
Nowoczesne technologie w dziedzinie destylacji rozpuszczalników rozwijają się w szybkim tempie, co pozwala na zwiększenie efektywności procesów oraz poprawę jakości uzyskiwanych produktów. Jednym z innowacyjnych podejść jest zastosowanie technologii membranowych, które umożliwiają separację składników bez konieczności podgrzewania cieczy. Dzięki temu możliwe jest znaczne obniżenie kosztów energetycznych oraz minimalizacja ryzyka degradacji wrażliwych substancji chemicznych. Innym przykładem nowoczesnych technologii jest wykorzystanie destylacji z wykorzystaniem ultradźwięków, która pozwala na przyspieszenie procesu separacji poprzez generowanie mikroskopijnych bąbelków powietrza w cieczy. To zjawisko zwiększa powierzchnię kontaktu między parą a cieczą, co prowadzi do szybszej i bardziej efektywnej separacji składników. Dodatkowo rozwijają się technologie automatyzacji procesów destylacyjnych, które pozwalają na precyzyjne monitorowanie i kontrolowanie warunków operacyjnych, co przekłada się na wyższą jakość i stabilność produkcji.
Jakie są różnice między destylacją a innymi metodami separacji
Destylacja rozpuszczalników to jedna z wielu metod separacji składników mieszanin, jednak różni się ona od innych technik pod względem zasad działania oraz zastosowań. Na przykład ekstrakcja to metoda oparta na różnicy rozpuszczalności składników w różnych rozpuszczalnikach. Jest to technika często stosowana w chemii organicznej do izolowania substancji czynnych z roślin czy innych źródeł naturalnych. W przeciwieństwie do destylacji, ekstrakcja nie wymaga podgrzewania ani skraplania pary, co sprawia, że jest bardziej odpowiednia dla substancji termolabilnych. Inną popularną metodą separacyjną jest chromatografia, która polega na rozdzielaniu składników na podstawie ich interakcji z fazą stacjonarną i ruchomą. Chromatografia oferuje wysoką selektywność i może być stosowana do analizy bardzo małych ilości substancji. Jednakże jej zastosowanie w przemyśle może być ograniczone przez czasochłonność oraz koszty związane z przygotowaniem kolumn chromatograficznych. W porównaniu do tych metod, destylacja jest bardziej odpowiednia dla dużych skali produkcji oraz sytuacji wymagających uzyskania wysokiej czystości produktów końcowych.
Jakie są kluczowe czynniki wpływające na efektywność destylacji rozpuszczalników
Efektywność procesu destylacji rozpuszczalników zależy od wielu czynników, które należy uwzględnić podczas projektowania i przeprowadzania tego typu operacji. Przede wszystkim kluczową rolę odgrywa temperatura wrzenia poszczególnych składników mieszaniny. Różnice w temperaturach wrzenia pozwalają na skuteczną separację składników poprzez ich parowanie i skraplanie. Im większa różnica temperatur wrzenia między składnikami, tym łatwiejsza będzie ich separacja. Kolejnym istotnym czynnikiem jest ciśnienie atmosferyczne panujące w systemie; obniżenie ciśnienia może zmniejszyć temperaturę wrzenia substancji, co pozwala na oddzielanie ich bez ryzyka degradacji termicznej. Ważnym aspektem jest także konstrukcja kolumny destylacyjnej; jej wysokość oraz rodzaj użytych materiałów mają wpływ na efektywność procesu poprzez zwiększenie powierzchni kontaktu między parą a cieczą. Dodatkowo prędkość przepływu pary oraz cieczy również wpływa na wydajność procesu; zbyt szybki przepływ może prowadzić do niedostatecznej separacji składników.
Jakie są przyszłe kierunki badań nad destylacją rozpuszczalników
Przyszłość badań nad destylacją rozpuszczalników zapowiada się obiecująco dzięki rosnącemu zainteresowaniu nowymi technologiami oraz metodami optymalizacji procesów przemysłowych. Jednym z głównych kierunków badań jest rozwój bardziej efektywnych systemów separacyjnych opartych na nanotechnologii i materiałach kompozytowych, które mogą znacząco zwiększyć wydajność procesów destylacyjnych poprzez poprawę właściwości transportowych i selektywności membranowych systemów separacyjnych. Inny istotny obszar to badania nad zastosowaniem zielonych technologii w procesach destylacyjnych; poszukiwanie alternatywnych rozpuszczalników oraz metod redukcji zużycia energii staje się coraz ważniejsze w kontekście ochrony środowiska oraz zrównoważonego rozwoju przemysłu chemicznego. Dodatkowo rozwój sztucznej inteligencji i uczenia maszynowego otwiera nowe możliwości w zakresie optymalizacji procesów produkcyjnych; algorytmy mogą analizować dane operacyjne i dostosowywać parametry procesu w czasie rzeczywistym dla uzyskania lepszych wyników jakościowych i wydajnościowych.